At present, the specifications as well as the varieties of laser lenses on the market are numerous, and the price is also uneven, specifically the difference between the materials used in these lenses as well as the price difference is reflected in where?
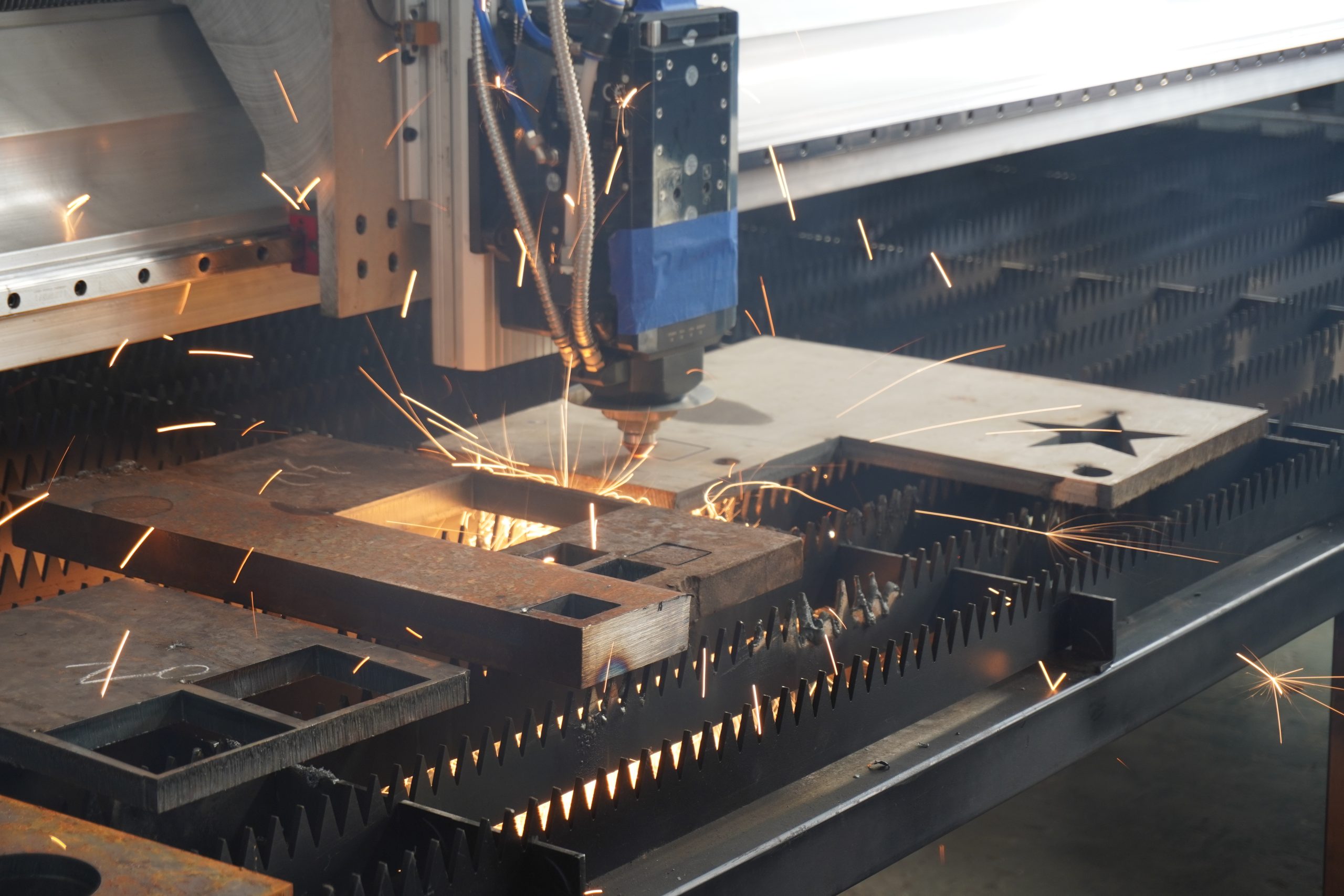
Currently, the market offers a wide variety of laser optics, with varying specifications and prices. The differences in material composition of these optics directly contribute to the price variations. Below, we provide a detailed introduction to the optical substrates used in these lenses:
Optical Glass (BK7/K9)
BK7 (or K9) is a commonly used borosilicate crown glass with a transmission range from 380nm to 2100nm. It has high homogeneity, low bubble and impurity content, making it suitable for transmission optical applications. BK7 also has high hardness and excellent scratch resistance. However, it has a relatively high thermal expansion coefficient, which makes it unsuitable for temperature-sensitive applications.
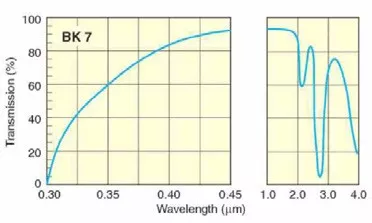
Due to its susceptibility to thermal expansion and potential cracking at high temperatures, BK7 (K9) is rarely used in laser cutting applications. Despite its lower cost, it is commonly used in low-power (≤500W) laser welding fields.
Fused Silica
In China, fused silica materials are classified into JGS1, JGS2, and JGS3, each for different applications:
- JGS1: Primarily used in the ultraviolet (UV) and visible light ranges, this material is free from bubbles and impurities.
- JGS2: Typically used as a mirror substrate; it contains a higher number of small bubbles.
- JGS3: Known for its excellent infrared transmission, but it has a higher concentration of bubbles, limiting its broader application.
Fused silica, particularly UV-grade fused silica, is an extremely pure, amorphous form of silicon dioxide with a transmission range from 185nm to 2300nm. This non-crystalline, colorless quartz has a very low thermal expansion coefficient and excellent optical properties. Its transmission and homogeneity surpass crystalline forms of quartz (e.g., crystal quartz). Fused silica also has a high damage threshold, making it ideal for high-energy laser applications. Its high refractive index uniformity and low impurity content make it suitable for both transmission and reflection optical systems, especially in high-energy optical systems.
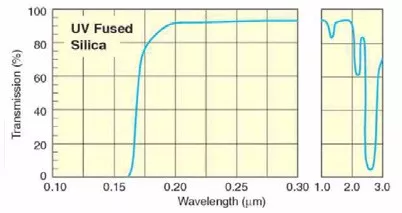
In laser cutting, fused silica is used to manufacture various optical components. Compared to BK7, it is better suited for applications requiring higher transmission rates and higher damage thresholds. Depending on the specific characteristics of the fused silica materials, JGS1 is superior to JGS2, which in turn is better than JGS3.
Pricing Considerations
JGS1 fused silica is expensive, while JGS2 is relatively more affordable but contains bubbles. Therefore, JGS2 is more commonly used in the market for manufacturing medium-to-low-power laser optics due to its high cost-effectiveness. It meets the requirements of lower-grade cutting applications, but its performance in medium-to-high power laser cutting is significantly lower. To achieve better results in these applications, JGS1 is typically preferred, as it provides more consistent and stable performance.
Coating Differences
In addition to differences in substrate materials, coatings on optical lenses play a crucial role in their performance. Variations in coating equipment, materials, ratios, and coating duration significantly affect the lens’s transmission rate, service life, and overall performance. Therefore, when selecting laser optics, it is not only the price that matters but also the quality of the lenses that should be prioritized. Quality should always be the key consideration.