With the rapid popularization of new energy vehicles, manufacturing technology is gradually developing in the direction of high precision, high efficiency and intelligence. Precision laser processing as one of the advanced manufacturing technologies, with its high precision, low loss and other characteristics, is playing an important role in the production process of new energy vehicles, especially in the battery manufacturing, lightweight body and internal and external parts processing and other aspects of outstanding performance. This paper will discuss in detail the specific application of precision laser processing in the field of new energy vehicles, and look forward to its future development prospects.
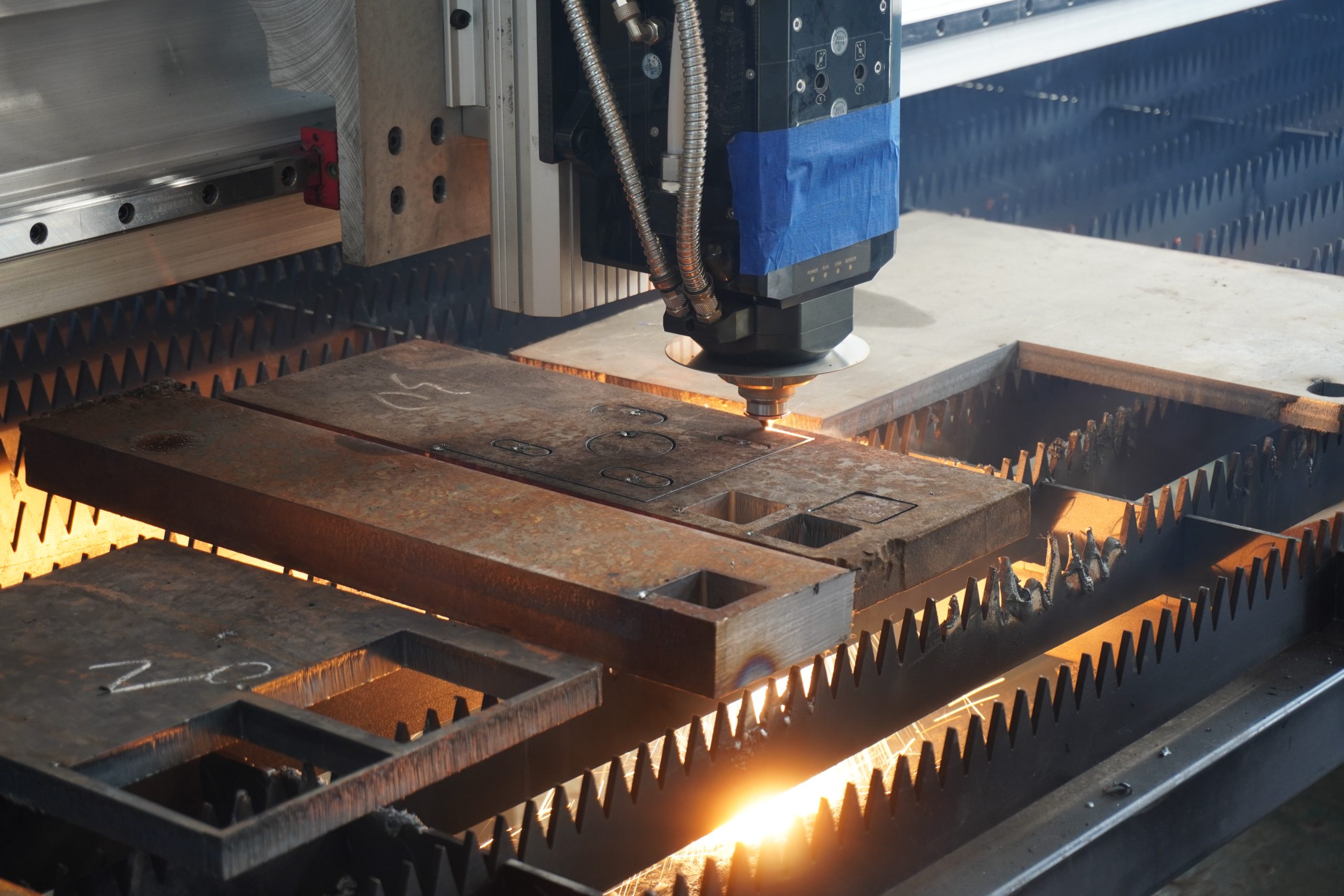
PART 01 Overview of Precision Laser Processing Technology
1.1 Definition and Characteristics of Precision Laser Processing
Precision Laser Processing is a technology that utilizes high energy density laser beams to locally heat, melt or cut materials. Its main features include:
- High precision: laser processing can realize micron or even nanometer precision control.
- Non-contact processing: no mechanical contact occurs during processing, reducing the loss of material.
- Strong controllability: laser power, wavelength, pulse width and other parameters can be precisely adjusted to adapt to different processing needs.
1.2 Classification of Precision Laser Processing
Common precision laser processing technologies include laser cutting, laser welding, laser marking and laser cleaning. These technologies can be widely used in the processing of different materials, structures and parts, and are applicable to a variety of scenarios in the field of new energy vehicles.
PART 02 Requirements of New Energy Vehicles on Manufacturing Technology
2.1 High Precision and High Reliability
High-density batteries and sensitive electronic components are used in a large number of new energy vehicles, so the parts and components are required to have high precision and high reliability in order to ensure the stable performance of the whole vehicle.
2.2 Lightweight Demand
In order to improve the range, the new energy vehicle industry is paying more and more attention to the application of lightweight materials, which puts forward extremely high requirements for the processing process, which is required to minimize the loss of materials and weight increase in the processing process.
2.3 Intelligent and Green Manufacturing
Under the trend of intelligent manufacturing and green manufacturing, the high energy efficiency and low pollution characteristics of laser processing fit the development needs of new energy vehicles.
PART 03 Application of Precision Laser Processing in New Energy Vehicle Battery Production
3.1 Cutting and Welding of Battery Pole Pieces
In the production of power batteries, laser cutting and welding technology is used in the processing of battery structural parts such as pole pieces and lugs, which has the advantages of high precision and low heat impact. Precision laser cutting of battery pole pieces can effectively reduce edge burrs, thus improving the energy density and safety of the battery.
3.2 Laser Welding of Battery Modules and Battery Packs
Laser welding technology is widely used in the encapsulation of battery modules and the assembly of battery packs, which can achieve uniform and stable welding effects and effectively improve the structural strength and durability of batteries. In addition, laser welding has a high degree of automation, can be seamlessly connected with the production line to improve production efficiency.
PART 04 Application of Precision Laser Processing in New Energy Vehicle Body and Structural Parts
4.1 Laser Cutting and Welding of Lightweight Body Materials
New energy vehicles are widely used in lightweight body materials such as aluminum alloys, carbon fibers, and high-strength steels, and the processing of these materials often requires high precision and special welding processes. Precision laser cutting and welding technology is particularly suitable for the processing of lightweight body structures due to its high energy density and refinement characteristics. Laser cutting and welding not only reduces the weight of the body, but also improves the crashworthiness and durability of the entire vehicle.
Laser welding of aluminum alloy body parts: Aluminum alloy material has high reflectivity and thermal conductivity, traditional welding process is prone to cracks, while laser welding can avoid cracks and welding defects and improve the quality of welds through precise control of heat input.
Laser cutting of carbon fiber materials: Carbon fiber composites are used in new energy vehicle bodies and frames, but cutting is difficult. Laser cutting, due to its high energy density, can accomplish high-quality cutting with reduced thermal impact on the material.
4.2 Application of laser in chassis structural parts of new energy vehicles
Chassis is a key component of new energy vehicle structure, which needs to have high strength and lightweight characteristics. Precision laser cutting and welding technology can meet the complex molding needs of chassis structural components. For example, in the processing of suspension systems and axles and other structural components, laser welding can ensure the quality and strength of the weld, increasing the durability and safety of the vehicle.
PART 05 Application of Precision Laser Processing in Interior and Exterior Parts of New Energy Vehicles
5.1 Laser Marking and Micro-hole Processing of Interior Parts
Laser marking technology is widely used in interior parts, which can realize exquisite marking and pattern engraving on various materials. For example, the pattern of the steering wheel and instrument panel, the logo of the air conditioning vents, can be completed by laser marking. At the same time, micro-hole processing in the interior, such as the speaker holes of the audio system, can also use laser technology to complete high-precision perforation operations to enhance the overall sophistication and comfort of the car interior.
5.2 Laser Cleaning and Surface Treatment of Exterior Parts
Laser cleaning technology can efficiently remove oil, oxidized layer and other impurities on the metal surface, and prepare for the subsequent spraying, plating and other processes. In the processing of new energy vehicle exterior parts, laser cleaning can replace the traditional chemical cleaning, with environmental protection and high efficiency. In addition, the laser can also be used for surface finishing processing of exterior parts, by changing the surface texture, to improve the decorative effect and durability of the parts.
PART 06 Application of Precision Laser Processing in Electronic Components of New Energy Vehicles
6.1 Laser Precision Welding of Electronic Components
New energy vehicles contain a large number of electronic control modules and sensors, and these components have extremely high requirements for welding precision. Laser welding technology has irreplaceable advantages in the welding of these electronic components. For example, in the production of battery management systems and electric drive systems, laser welding ensures firmness and stability at the joints and reduces the risk of poor electrical contact.
6.2 Laser micromachining of electronic components
The production process of some electronic components in new energy vehicles, such as circuit boards and connectors, requires precise micromachining. Laser micromachining can realize the engraving of complex graphics and the processing of fine holes without touching the material, which is suitable for the miniaturization and high-density integration of electronic components in new energy vehicles.
PART 07 Summary of the advantages of precision laser processing in the field of new energy vehicles
Precision laser processing can effectively meet the manufacturing needs of new energy vehicles due to its advantages of high efficiency, environmental protection and flexibility. Specific advantages include:
- High precision: laser processing can achieve micron-level precision to meet the production needs of precision parts for new energy vehicles.
- Non-contact: avoiding mechanical damage and prolonging the service life of parts.
- High automation: Laser equipment can be integrated with automated production lines to improve production efficiency.
- Green environmental protection: laser processing process has almost no pollutant emissions, in line with the concept of green manufacturing.
PART 08 Development Prospects of Precision Laser Processing in the Field of New Energy Vehicles
8.1 Technological Innovation Driving Application Upgrade
With the continuous progress of laser technology, new technologies such as ultra-fast laser, fine beam control and so on will promote the further application of laser processing in the field of new energy vehicles. In the future, laser processing may realize higher precision, lower heat impact and faster production speed to meet more demanding processing needs.
8.2 Laser Processing in the Trend of Intelligent Manufacturing
Under the trend of intelligent manufacturing, the level of intelligence and automation of laser processing equipment will be further improved, and the use of machine vision and artificial intelligence technology can realize adaptive processing, real-time monitoring and quality feedback, and improve the degree of intelligence in the production of new energy vehicles.
8.3 Green Manufacturing Trend Boosts the Popularization of Laser Processing
With the continuous strengthening of environmental protection regulations, laser processing will be more widely used in the production of new energy vehicles due to its non-polluting and low-energy consumption characteristics, and help the automobile manufacturing industry to develop in a green and sustainable direction.
PART
08
Development Prospects of Precision Laser Processing in the Field of New Energy Vehicles
8.1 Technological Innovation Driving Application Upgrade
With the continuous progress of laser technology, new technologies such as ultra-fast laser, fine beam control and so on will promote the further application of laser processing in the field of new energy vehicles. In the future, laser processing may realize higher precision, lower heat impact and faster production speed to meet more demanding processing needs.
8.2 Laser Processing in the Trend of Intelligent Manufacturing
Under the trend of intelligent manufacturing, the level of intelligence and automation of laser processing equipment will be further improved, and the use of machine vision and artificial intelligence technology can realize adaptive processing, real-time monitoring and quality feedback, and improve the degree of intelligence in the production of new energy vehicles.
8.3 Green Manufacturing Trend Boosts the Popularization of Laser Processing
With the continuous strengthening of environmental protection regulations, laser processing will be more widely used in the production of new energy vehicles due to its non-polluting and low-energy consumption characteristics, and help the automobile manufacturing industry to develop in a green and sustainable direction.
Summary
The application of precision laser processing in the field of new energy vehicles is becoming more and more widespread, which not only improves the processing accuracy and quality of parts, but also promotes the process of lightweight and green manufacturing of new energy vehicles. In the future, with the continuous development of laser technology and intelligent manufacturing, laser processing will play a more critical role in the manufacturing of new energy vehicles, injecting new vitality for the sustainable development of the industry.